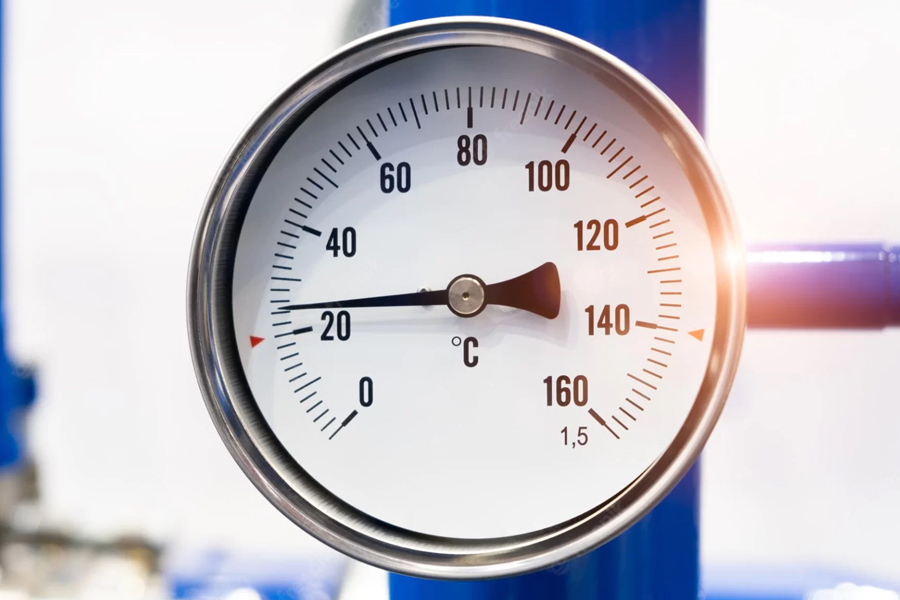
¿Qué es la calibración de termómetros y por qué es clave en la industria?
La calibración de termómetros es un proceso técnico mediante el cual se compara la lectura de un termómetro con un patrón de referencia, que ha sido previamente certificado y que garantiza una medición precisa de la temperatura. Este procedimiento es esencial para asegurar que los equipos de medición estén operando dentro de los márgenes permitidos de error, especialmente en entornos industriales donde un desvío mínimo en la lectura puede representar pérdidas económicas, riesgos para la seguridad o incumplimientos normativos.
En sectores como el gas, la industria petroquímica, la producción alimentaria o los laboratorios farmacéuticos, el control exacto de la temperatura no es solo una exigencia técnica, sino un requisito legal. Las autoridades regulatorias y los sistemas de gestión de calidad, como ISO 9001, exigen que todos los instrumentos de medición sean verificados y calibrados de forma periódica para mantener la confiabilidad de los procesos.
Tipos de termómetros y su necesidad de calibración
La calibración de termómetros no se limita a un solo tipo de instrumento. En el mercado existen múltiples modelos que requieren atención personalizada según su aplicación, rango de trabajo y condiciones ambientales.
Entre los principales tipos de termómetros industriales encontramos:
- Termómetros digitales: ampliamente usados por su facilidad de lectura. Necesitan calibración periódica ya que su precisión puede degradarse con el tiempo.
- Termómetros de resistencia (RTD): conocidos por su alta exactitud, son ideales para aplicaciones críticas. Deben verificarse con patrones de alta precisión.
- Termopares: muy comunes en entornos de alta temperatura, como hornos o procesos metalúrgicos. Su calibración es compleja, pero esencial.
- Termómetros infrarrojos: usados en procesos sin contacto. Aunque cómodos, son propensos a errores si no se calibran adecuadamente con cuerpos negros de referencia.
- Termómetros de mercurio o alcohol: menos comunes actualmente, pero aún utilizados en algunas industrias tradicionales. Requieren comparaciones visuales con columnas patrón.
Cada tipo de termómetro tiene características únicas y su calibración debe considerar factores como la deriva del sensor, la exposición al ambiente y el rango de operación habitual.
Métodos de calibración: guía práctica paso a paso
El proceso de calibración de termómetros puede variar según el equipo y la normativa aplicada, pero existen procedimientos estándar que permiten asegurar una medición fiable. Procedimiento básico de calibración:
- Selección del patrón de referencia: Debe ser trazable a un laboratorio acreditado (como un patrón secundario o primario)
- Estabilización térmica: Tanto el termómetro como el patrón se colocan en un medio de temperatura estable (como un baño termostático o un horno de calibración).
- Comparación de lecturas: Se comparan los valores del termómetro en calibración con los del patrón. Se recomienda tomar múltiples puntos (por ejemplo, 0 °C, 50 °C, 100 °C).
- Cálculo del error: Se determina el desvío del termómetro respecto al patrón.
- Ajuste o corrección: Si el termómetro permite ajuste digital o mecánico, se corrige. En caso contrario, se documenta el error y se utiliza una tabla de corrección.
- Emisión de certificado: Se elabora un certificado de calibración donde se detallan los resultados y condiciones del ensayo.
En empresas como Trameco, se promueve que los equipos que forman parte de sistemas críticos sean verificados por laboratorios certificados, y que todo el personal entienda la importancia de trabajar con termómetros calibrados. “Muchos errores operativos no vienen del operario, sino del instrumento. Una calibración a tiempo puede evitar una crisis”, afirman desde su experiencia con clientes del sector petrolero y de procesos.
La importancia de la precisión térmica en entornos industriales
Un pequeño error de medición puede desencadenar consecuencias graves en muchos procesos industriales. Por ejemplo, en el curado de polímeros, si la temperatura no alcanza el punto exacto requerido, el producto final puede no tener la resistencia adecuada. En la industria alimentaria, una lectura incorrecta puede significar una cocción incompleta, lo que compromete la seguridad alimentaria.
Para Trameco, garantizar la precisión térmica forma parte de su compromiso con la calidad. “Nuestros clientes exigen soluciones confiables. No podemos permitirnos suministrar equipos que no estén perfectamente calibrados o que no puedan ser verificados en campo”, destacan desde su departamento técnico.
Por esta razón, muchos clientes industriales han adoptado rutinas internas de recalibración cada 3 o 6 meses, dependiendo del uso del equipo. Una cultura de mantenimiento preventivo siempre es más rentable que enfrentar las consecuencias de un fallo no detectado.
¿Cómo implementar un programa interno de verificación periódica?
Cualquier empresa industrial puede crear su propio sistema de control de instrumentos. Un programa de calibración debe incluir:
- Inventario actualizado de todos los equipos de medición.
- Cronograma de calibraciones (anual, semestral, mensual según criticidad).
- Registro de certificados y resultados anteriores.
- Responsables internos designados.
- Protocolo para enviar equipos a laboratorios externos si es necesario.
Una empresa como Trameco, que maneja estándares internacionales en cada producto que suministra, sabe que un programa de este tipo no solo mejora la confiabilidad, sino que reduce costos a largo plazo.
Precisión, seguridad y confianza operativa
La calibración de termómetros no debe verse como un trámite más. Es una práctica esencial para cualquier organización que aspire a mantener altos estándares de calidad, seguridad y cumplimiento regulatorio. Las industrias modernas no pueden permitirse trabajar con datos térmicos imprecisos. Encuéntralos ahora dando Clic Aquí. Ponte en contacto con nosotros llamando al +511 271 2868 o dejándonos un mensaje al correo [email protected]. Ubícanos en la Av. Intihuatana 857, Santiago de Surco. ¡Te esperamos!